Recycling line how to understand?


Currently, several technologies allow to separate and then recycle the materials of Lithium batteries, each with their advantages.
So before going into the technique, what are the difficulties that can be encountered before and during the recycling of Lithium batteries.

The logistics imposed by transport regulations with very strict conditions make the recycling chain difficult. Complex necessarily means expensive, this is therefore an aspect to take into consideration before investing in a recycling line to choose the one that will be best suited.
A standard pallet for hazardous materials can cost more than €7,000, adding to that the cost of transporting the batteries.

A very high volume recycling line will certainly cost more in logistics than several lower volume recycling lines placed in different locations.

There are currently 2 ways to separate materials, the first by combustion and the second by grinding. Both technologies have advantages and disadvantages calculated on processing time and energy costs.
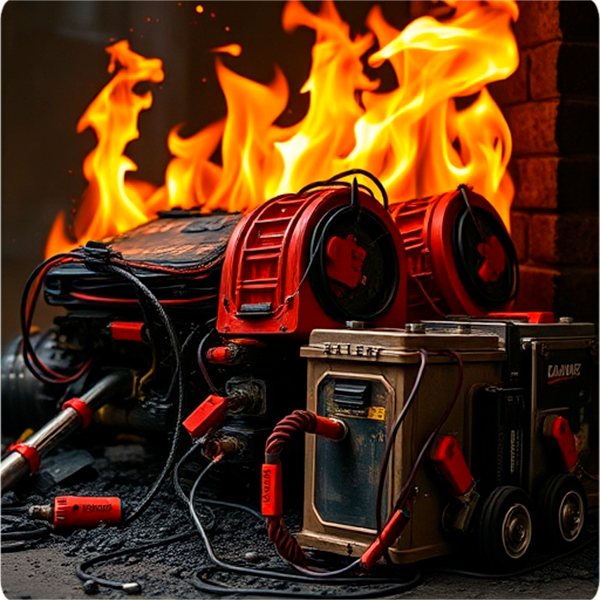
By combustion this method allows to go quickly and to have a recycling line in faster just-in-time with large volumes however the energy costs either by gas or electricity are greedy. It is not possible to be in balance on the energy cost of recycling with the logistics and that of the recovery of materials. The recycling costs are generally borne by the owner of the batteries. In this case the value of the initial battery is similar to the price of its recycling.

Crushing is an interesting solution to avoid the energy costs of recycling and also the sorting of recovering batteries that can be reused. The treatment of batteries will take longer given the attention that must be paid to them.
It is easy to make mistakes by making choices that are not adapted to the needs and it is important to be supervised by professionals who support all the needs and not just a part. Recycling, air treatment and landfill equipment are defined with specific needs because no standard can meet a global need, however the adjusted equipment will meet all needs without exception.
Now let's look at the separation of material by grinding.

The daily volume of batteries to be recycled or reconditioned is a determining factor in the type of recycling line.
Recycling lines are classified into 3 categories:
100Kgs/h = Discharging batteries and crushing
500Kgs/h = Discharge/Crushing or incineration
More 1T/h = Incineration

It is important to differentiate between dry and liquid batteries to better understand the recycling technique.
Lithium batteries are dry batteries where we will mainly find cobalt, steel, plastic, aluminum, copper and phosphate.
Acid batteries contain acids that will have to be treated differently with other equipment (different recycling line).
It is important to identify the type of batteries to be treated to adjust the recycling line to the needs because there is no standard each line is adjusted to the needs.
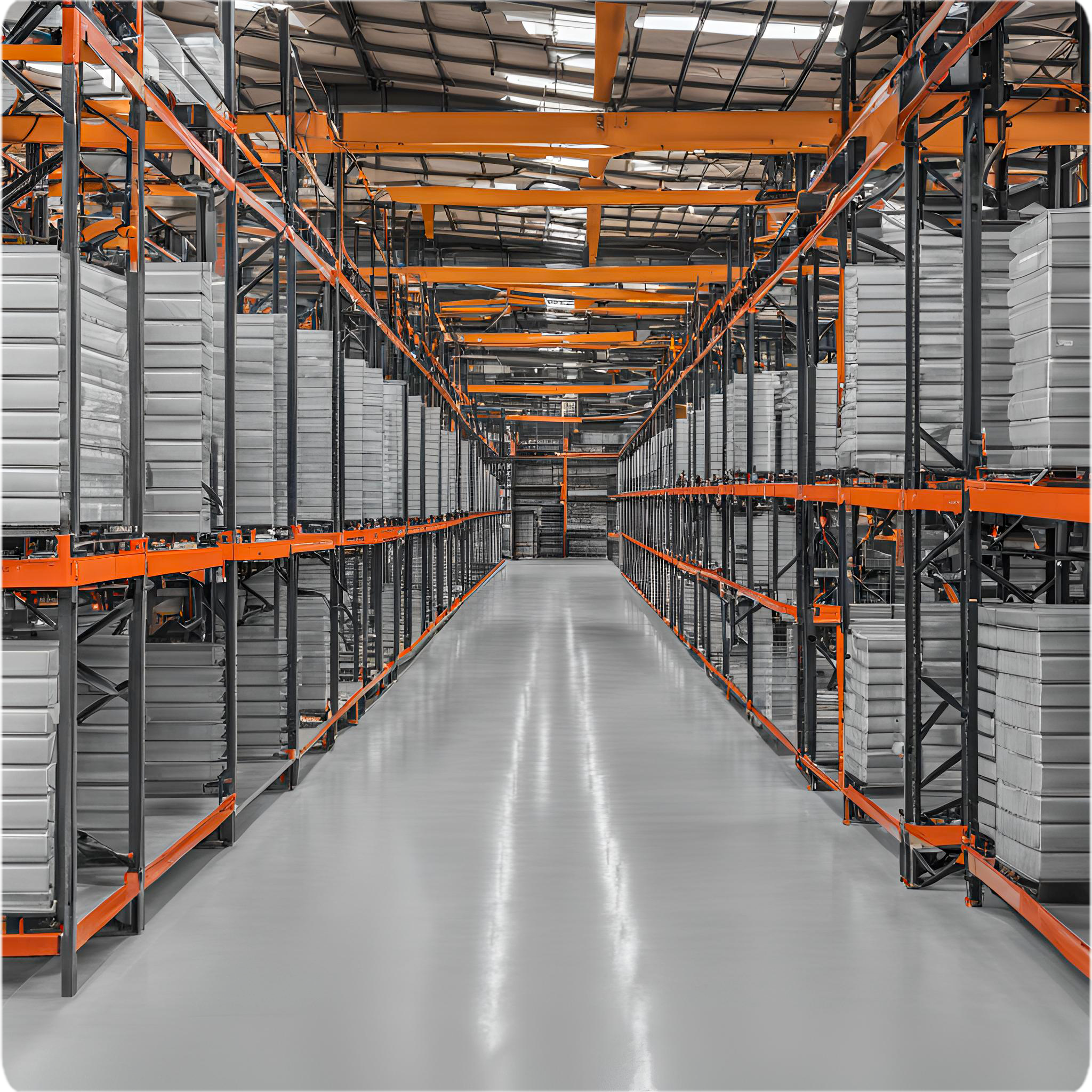
Storing batteries whether waiting for solutions or for recycling involves significant risks. For recycling it is important to adapt human and material resources to avoid risks whether human “accident” or material “fire”. ERP for the treatment of batteries before recycling are important and must be adapted without doing too much or not enough. Logistical equipment for example mobile cart or batteries can be placed on it will allow them to be moved at human height or on the ground Lithium batteries and even intervene on them without other handling.

The budget will depend on several points: the volume to be processed, the type of battery, the revaluation of materials or the return to the battery circuit and the recycling technology used. It is easy to quickly amortize a recycling line in the case where the material is recovered and the batteries can be put back on the market. This well-supervised activity with very few personnel trained in simple skills makes it possible to avoid significant logistics and subcontracting costs.

For better profitability, the discharge and crushing solution is without hesitation the best. However, suitable equipment is required that allows it to be below 0.3V to avoid the risk of a fire. The equipment must also allow the SOH and SOC to be assessed with test reports that improve the resale value. For this activity, qualified experts on both the recycling line and the discharge must accompany. These are qualified experts in the technologies, standards and operating procedures for lithium battery treatments that allow companies to be recognized as competent and qualified to develop their services.

The recycling line must be close to the storage and treatment part of the sorting and discharge of the cells but not too far from the air treatment system to avoid any risk of pollution. The incineration recycling lines for Lithium batteries are larger and require stricter anti-pollution rules than the recycling lines by discharges which are much less polluting. Each line can be adjusted with the available surface but preferably indoors. Expert professionals accompany with the layout and the electrical requirements necessary to form and operate the installation.
By incineration the process requires no specific handling apart from the separation of cells and modules in the battery. This procedure will still require safety equipment adapted to the personnel working on the dismantling line. The incineration of the battery will avoid the discharge cycle unlike crushing which will require several operations. The crushing of batteries requires more personnel before separation of materials but will allow a better recovery of recycling by the resale of reusable batteries and very low energy costs.